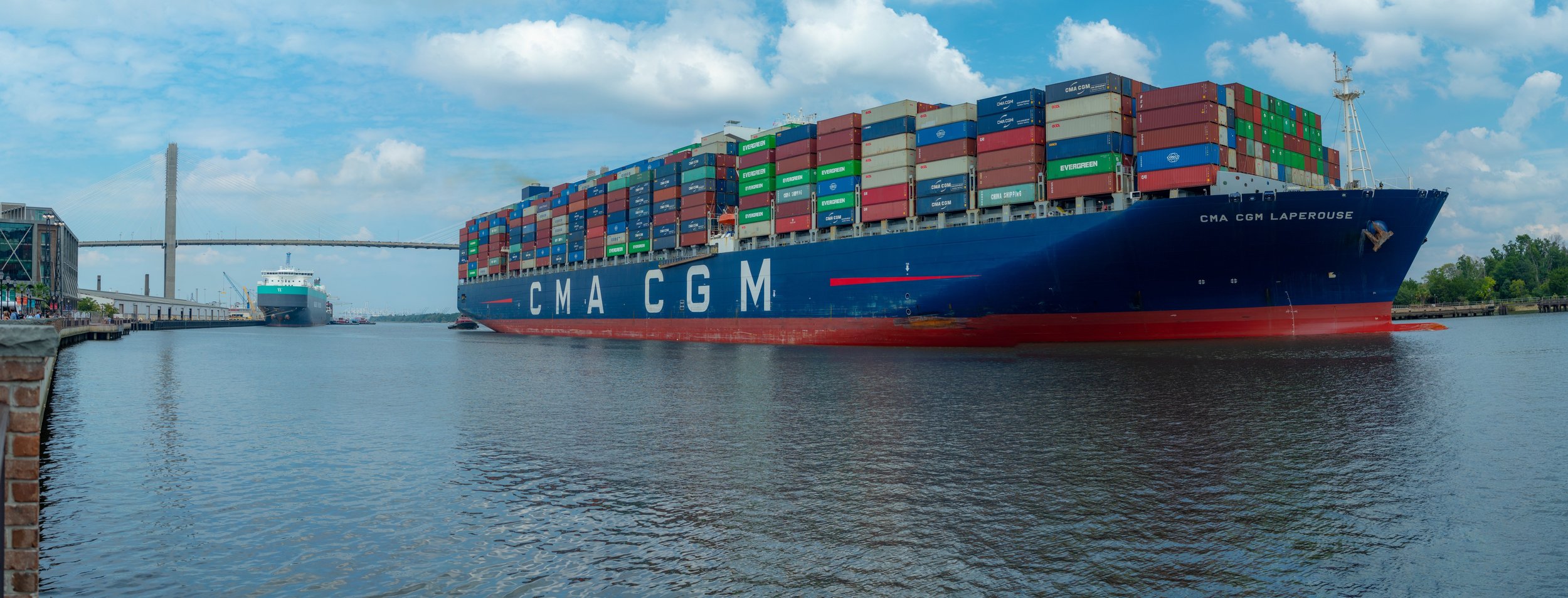
The message is as stark as it is simple — the roofing industry is experiencing a supply chain disruption that’s unlike any other in recent memory. And it’s going to be a while before it gets better. As with other supply issues, the main question asked, “Is this for real or just a ploy to raise pricing?” The answer is yes – it is very real.
A series of factors are to blame — none more striking than the COVID-19 crisis. Below are just a few examples of other factors that have compounded the effects from the pandemic (https://www.nrca.net/):
- Severe Weather Events: The 2021 winter storm Uri impacted the production of petroleum-based and other industrial chemicals throughout the Southwest. Most of the chemicals used to make many types of roofing membranes, insulation and adhesives come from this area of the U.S. The suddenness of the deep freeze resulted in not only shutting down factories but also caused damage to equipment and pipes transporting raw materials. The El Derecho storm, which impacted parts of the Midwest, caused further havoc and disruptions to trucking and logistics and required significant roofing volumes of roofing materials to repair the damage.
- Truck Driver Shortages: The trucking industry moves nearly 71% of all domestic freight. Driver personnel is woefully undersupplied, and the industry will need to hire 1.1M drivers to keep up with current demand.
- Global Logistics: Ports of entry worldwide are experiencing significant delays off-loading cargo ships. Some ports have experienced delays up to three weeks. The overall lag in turnaround has effectively reduced shipping capacity by over 5%. Air freight is experiencing unprecedented troubles as well. Capacity is down 12% and demand up 25%.
- Suez Canal Obstruction: As one of the world’s busiest trade routes, the canal’s obstruction prevented an estimated $9.6 billion worth of trade from occurring. The blockage delayed a range of raw materials from reaching the United States. Even though this trade route has been opened, the United States continues to be affected by the closure.
- Shipping Containers: There are not enough intermodal containers available to service the volume of goods to be shipped. Multiple factors have driven this situation including increased demand of consumer products during COVID, out of balance trade routes and inability of manufacturers to produce new units.
- Government Stimulus: With government aid, United States’ businesses and consumers have ramped up spending, adding to the already significant supply/demand imbalance.
- Labor Shortages: The Labor Shortage we are all dealing with, has made it increasingly harder to find labor and this has especially affected manufacturing facilities and the ability to secure and obtain raw materials.
While roofing contractors have experienced stressed supply lines before, this situation is uniquely different. A large challenge is that suppliers and contractors are not just dealing with raw material shortages for the waterproofing membranes. While every technology within the roofing space (PVC, TPO, EPDM, etc.) have faced shortages and rising costs of raw materials, what makes the industry unique is that you’re dealing with a complete system and not just supplying that top waterproofing layer. A full roof system can involve a large variety of products including adhesives, screws and plates, gypsum boards, vapor barriers, etc.
Unfortunately, it’s not just the roofing materials. The new and replacement window market for housing is currently in shambles as COVID-19 labor manufacturing constraints persist. This is also the case for vinyl siding, resins and any steel related items. All the manufacturers of these system components are also dealing with supply issues and rising costs of raw materials.
So, what does this mean for all of us involved in the construction industry and especially roofing? The most important thing we can all collectively do is work together closely, communicate, and strategically plan out projects. Setting realistic and clear expectations that costs will be higher and timelines will be longer is the key to planning with our customers. Having open channels of communication and strong partnerships between the suppliers, installers, insurance agents and homeowners can only help increase the successful completion of projects, as well.
Eventually things will settle down, but for now, the more we work together and communicate, the better we can all successfully navigate these current challenges.